Comparing Fulfillment Costs: In-House vs. Outsourced
- jaykim73
- May 10, 2024
- 2 min read
Updated: Jan 30
Comparing Fulfillment Costs: In-House vs. Outsourced
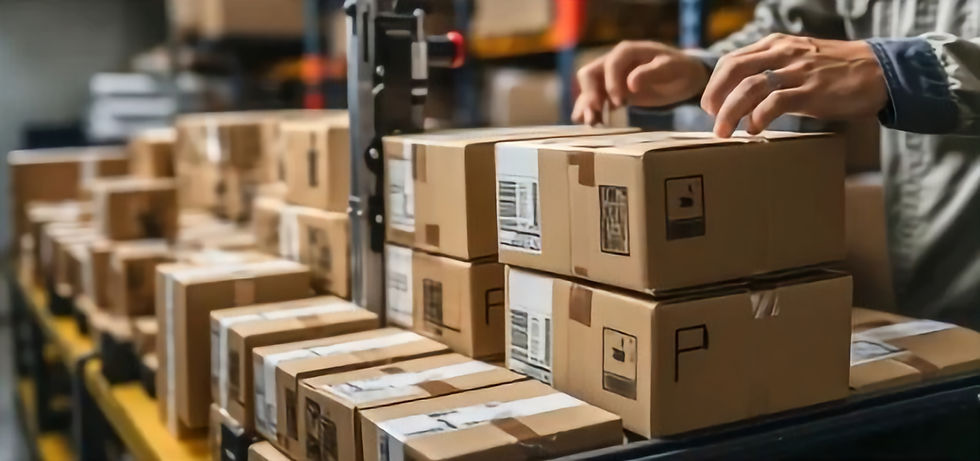
When it comes to fulfillment, businesses often weigh the pros and cons of fulfillment cost of in-house operations versus outsourced to third-party providers. Understanding the cost implications of each option is crucial for making an informed decision that aligns with your business goals. Let's explore the financial aspects of both in-house and outsourced fulfillment to help you determine the best approach for your company.
Cost Considerations: In-House vs. Outsourced Fulfillment
In-House Fulfillment:
Warehouse Expenses: Renting or buying warehouse space incurs costs related to utilities, security, and insurance.
Labor Costs: Employing and managing staff for fulfillment tasks adds to operational expenses.
Infrastructure Costs: Investment in equipment and maintenance, including technology like AI for logistics.
Overhead Costs: Additional charges for facility upkeep and other operational necessities.
Outsourced Fulfillment:
Service Costs: Third-party providers may charge fees for their fulfillment services.
Delivery Fees: Consider negotiated shipping rates and any associated delivery charges.
Storage Fees: Cost of storing inventory in third-party warehouses.
Extra Fees: Additional charges for packaging, specialty services, or peak periods.
Pros and Cons of Outsourced Fulfillment:
Pros:
Cost-Effectiveness: Outsourcing can reduce costs associated with internal infrastructure and labor.
Focus on Core Competencies: Allows internal teams to concentrate on core business activities.
Scalability: Flexibility to scale operations based on business growth without significant upfront investment.
Access to Expertise: Utilize the specialized knowledge and technology of fulfillment experts.
Cons:
Loss of Control: Outsourcing may entail relinquishing some control over the fulfillment process.
Communication Challenges: Collaborating with external partners may lead to communication issues.
Dependency: Operations become reliant on third-party performance, which can pose risks.
Quality Concerns: Ensuring that outsourced providers meet quality standards requires ongoing monitoring.
Choosing the Right Solution
Deciding between in-house and outsourced fulfillment depends on various factors such as business size, budget, and desired level of control. In-house operations offer direct control but require significant investments in infrastructure and management. Outsourcing provides convenience and scalability but may involve trade-offs in control and quality assurance.
Key Considerations for Choosing Fulfillment Solutions:
Warehousing Costs: Evaluate the expenses associated with warehouse storage to ensure they fit within your budget and meet storage needs.
Shipping Discounts: Consider shipping rates negotiated by fulfillment partners to optimize cost-effectiveness.
Pick and Pack Fees: Understand labor and material costs involved in preparing orders for shipping.
Hourly Rates: Compare hourly labor costs for in-house operations against the cost structure of outsourcing to determine the most affordable option.
Optimizing Your Fulfillment Strategy:
Choosing the right fulfillment solution is essential for optimizing your business operations. By assessing your specific requirements and considering the benefits of different fulfillment approaches, you can tailor a solution that aligns perfectly with your goals. Reach out to discuss your fulfillment needs and explore customized solutions for your business.
Click here to learn more about Comparing Fulfillment Costs: In-House vs. Outsourced.
Comments